Advanced charging system technology
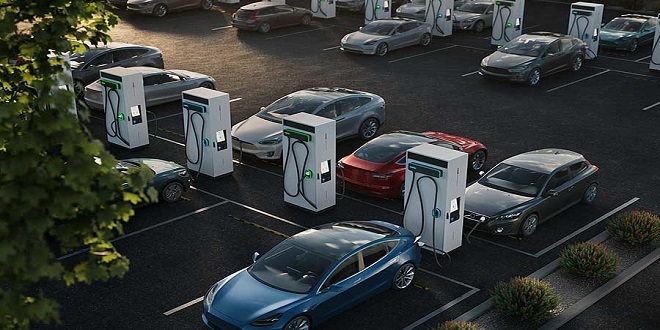
Charging system – problems and solutions
The charging system of a vehicle has to cope under many varied conditions. An earlier section gave some indication as to the power output that may be required. The first scenario is a traffic jam, on a cold night, in the rain! This can involve long periods when the engine is just idling, but the use of nearly all electrical devices is still required.
The second scenario is that the car has been parked in the open on a frosty night. The engine is started, and seat heaters, heated rear window, and blower fan are switched on whilst a few minutes are spent scraping the screen and windows. All the lights and wipers are now switched on and a journey of half an hour through busy traffic follows. The seat heaters and heated rear window can generally be assumed to switch off automatically after about 15 minutes.
The five possible options listed above have some things in their favor and some against, not least of which are the technical and economic factors. For the manufacturers, I would predict that a combination of a more powerful alternator, which can be run at a higher speed, together with a higher or dual voltage system, would be the way forward. This is likely to be the most cost-effective and technically feasible solution. Each of the suggestions is now discussed in more detail. The easiest solution to the demand for more power is a larger alternator, and this is, in reality, the only method available as an after-market improvement. It must be remembered, however, that power supplied by an alternator is not ‘free’. For each watt of electrical power produced by the alternator, between 1.5 and 2 W are taken from the engine due to the inefficiency of the energy conversion process. An increase in alternator capacity will also have implications relating to the size of the drive belt, associated pulleys, and tensioners.
Charge balance calculation
The charge balance or energy balance of a charging system is used to ensure that the alternator can cope with all the demands placed on it and still charge the battery. The following steps help to indicate the size of alternator required or to check if the one fitted to a vehicle is suitable. As a worked example will be used. The calculations relate to a passenger car with a 12 V electrical system. A number of steps are involved.
Alternator characteristics
Alternator manufacturers supply ‘characteristic curves for their alternators. These show the properties of the alternator under different conditions. The curves are plotted as output current, against alternator rev/min and input power against input rev/min.
The power curve is used to calculate the type of drive belt needed to transmit the power or torque to the alternator. As an aside, the power curve and the current curve can be used together to calculate the efficiency of the alternator.
Mechanical and external considerations
Most light vehicle alternators are mounted in similar ways. This usually involves a pivoted mounting on the side of the engine with an adjuster on the top or bottom to set drive belt tension. It is now common practice to use ‘multi-V’ belts driving directly from the engine crankshaft pulley. This type of belt will transmit greater torque and can be worked on smaller diameter pulleys or with tighter corners than the more traditional ‘V’ belt.
Last word
The drive ratio between the crank pulley and alternator pulley is very important. In simple terms, the alternator should be driven as fast as possible at idle speed, but must not exceed the maximum rated speed of the alternator at maximum engine speed.